Food processors talk about regulatory issues, workforce needs
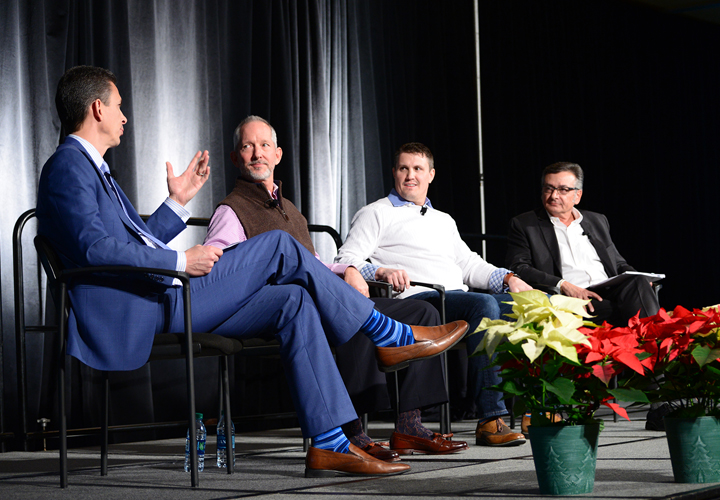
The Springfield region has always had strong agricultural roots, but many don’t recognize the strength and importance of agribusiness to the area’s manufacturing sector. Those businesses were on full display during the 2016 Manufacturing Outlook, held at University Plaza on December 7.
Joe Reynolds, president of Central States Industrial and of the SBDC Board of Directors, led a panel of representatives from two long-time employers and one exciting new addition to the area’s manufacturing sector. The panel included Kurt Hellweg, chairman of International Dehydrated Foods, Inc.; Jeff Hinds, vice president of food safety, quality assurance, compliance and grower support with Vital Farms; and Randy Tucker, manager of human resources for Dairy Farmers of America.
The panelists hit a number of topics such as the Food Safety Modernization Act, created in 2011 with the intent of reducing the risk of foodborne illnesses. The Centers for Disease Control estimates that 48 million people get sick and 3,000 die each year from foodborne diseases.
All the panelists were in agreement that while reducing illness is a significant task, their companies likely will not feel much effect from the regulations because they already meet the requirements.
“Companies that have been diligent in their processes have been leading this charge,” Hinds said. “If companies have been doing things the right way all along, there shouldn’t be much impact.”
Panelists also discussed current and future consumer trends, which they feel will include a push for more organic and homegrown foods and healthier options, as well as a commensurate increase in price.
“More people want to know the story behind their food, and there will be willingness to pay a premium price for a more premium product,” Hellweg said.
But perhaps the biggest takeaway was how other manufacturers and the overall business community can support agribusiness. The main issue for the panelists is one that plagues nearly every business sector: workforce training.
Hellweg said continued evolution of manufacturing processes means more machines and fewer people doing the actual creation … but the need for people remains. “We’re going to need programmers, welders, technicians to repair the machines,” he said.
These needs are part of the reason the Chamber continues to focus its efforts on a variety of workforce readiness, education and training programs for people ranging from school children to experienced members of the adult workforce.
The need goes beyond industry-specific training; soft skills such as writing and comprehension of instructions also are in high demand—and Tucker notes that those skills have to be taught early. “Technology drives what we do, but there will always be a human element. We need people who can ensure the product is produced the right way and meets the right specification,” he said. “And by the time kids get to high school, it’s too late to start teaching them those things. It has to start earlier.”
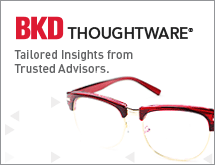